How heavy industry should tackle the digital transformation imperative
In a world where the likes of automation, data mining and tech-powered solutions are no longer maybes but musts for businesses, digital maturity has become a key predictor of success. Defined as the measure of an organisation’s ability to create value through digital1, it captures the likelihood of businesses benefiting from their digital transformation efforts and, crucially, shines a spotlight on those likely to struggle due to low levels of digital maturity.
And the news is not good for heavy industries.
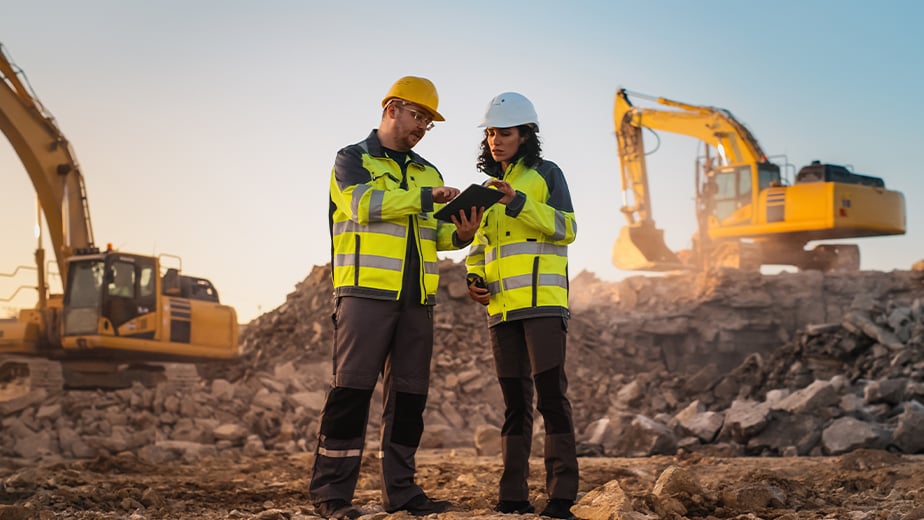
According to BCG’s Digital Acceleration Index, a diagnostic tool that measures and compares companies’ digital capabilities, the metals and mining industry is up to 40% less digitally mature than similar sectors2. In a similar vein, a McKinsey survey found only 4% of respondents from the heavy industry sector had captured significant bottom-line improvements from their efforts to automate and, of greater concern, more than half believed it would take up to three years to realise any benefits – or didn’t even know if they would3.
For some readers, it will not come as a surprise that some organisations in the heavy industry are struggling to implement digital transformation. Those familiar with the sector know there are several unique hurdles for executives and their teams to overcome in their quest for digital change including:
- Workforces tending to be blue-collar, which means they are often less familiar with digital solutions than other sectors
- Operations often being based in remote locations that have poor network bandwidth, along with rugged terrain making deployment of digital sensors difficult
- Cultural resistance to replace legacy systems
- Staff fears that the likes of automation could lead to workforce redundancies; and
- A lack of digital expertise among current executives and managers.
It is one thing to be aware of the hurdles and another to develop a strategy capable of overcoming them. In a bid to help heavy industry companies do just that, this article will highlight the risks of not fully embracing digital transformation, the need for a tailored approach to adoption and the benefits of partnering with a specialist tech partner to unlock one’s digital potential.
Why digital transformation is essential for heavy industry
Organisations that fail to embrace digital innovation are putting themselves at risk of hindering growth and falling behind competitors. Common concerns include:
- Misalignment between business needs and available solutions: a common challenge arises from the gap between off-the-shelf products and the specific requirements of heavy industry processes. This misalignment often results in suboptimal solutions that fail to address critical business needs, further complicating operations.
- Lack of visibility and actionable insights: the proliferation of disparate applications, Excel spreadsheets and emails often leads to a lack of real-time visibility and actionable metrics across the end-to-end process. Without comprehensive insights, decision-making becomes arduous and prone to errors.
- Standardisation of competency: heavy industries grapple with the issue of non-standardisation, where diverse interpretations of processes by individual engineers lead to inconsistent outcomes. Establishing clear guide rails and validation using technology and standardised processes is imperative to ensure competency across the workforce and foster organisational cohesion.
- Siloed applications and time wastage: teams frequently find themselves bogged down by menial tasks due to the inability of applications to communicate effectively with one another. This disconnect not only wastes valuable time but prevents skilled professionals from allocating their expertise towards value-added activities.
- Human limitation to monitor and action data: the challenge of identifying and raising critical insights in a timely manner for appropriate action poses a significant hurdle. The complexity of data makes it challenging for humans to monitor effectively, necessitating intelligent automation for timely intervention and decision-making.
- Excel sheet chaos: many organisations still rely heavily on Excel sheets riddled with complex macros and often understood by only a handful of team members. These convoluted spreadsheets churn out calculations but lack transparency and scalability. Do the processes you oversee have multiple Excel sheets stored on employees’ desktops and SharePoint and are they actually improving the process or making it more complex?
- Legacy applications and data disarray: legacy systems present a significant challenge frequently encountered in heavy industries, with vital operational data also residing within these aged systems. Compounding this issue is the fragmented nature of data distribution across multiple non-integrated systems, resulting in inefficiencies within processes. Nevertheless, the advent of modern automation technologies, when integrated with these legacy applications, offers a solution by bridging these gaps to improve the processes and minimise costs.
- Automation anxiety: despite the potential benefits, the fear of disrupting business-critical processes often deters organisations from embracing automation. This reluctance stems from a lack of understanding of how automation can be seamlessly integrated into existing workflows without causing upheaval.
- Approvals and audit: in an age where digital communication reigns supreme, many organisations still rely heavily on email for crucial communications and approval workflows. The result? An overwhelming influx of emails that are scattered across inboxes, making it challenging to track and retrieve critical information for audits or compliance purposes.
- Skill dependency: the perceived complexity of processes often leads to a heavy reliance on highly skilled personnel. This not only creates bottlenecks but limits scalability and agility as the expertise of these individuals becomes a single point of failure.
Why it pays to partner with digital transformation experts
The complexities involved in the vast landscape of heavy industries cannot be understated. For some, it involves planning and drilling wells in the oil and gas sectors. For others, it means managing the complex operation of travel and accommodation for FIFO workers or applying for land access permits and approvals. It is a credit to those employed in heavy industries that they are so highly qualified to navigate such complex scenarios.
Conversely, the same organisations are not typically experts when it comes to digital transformation. In the rush to counter the concerns outlined above, the last thing executives and managers should do is rush to roll out automation solutions or throw money at tech projects they do not understand. Likewise, inertia can be a concern for those who move too slowly for fear of getting it wrong.
Quality digital transformation requires a strategic vision, appropriate governance measures and ultimately the input of experts who are highly qualified in their own field. Just as heavy industry organisations invest in people who know their heavy industry, it pays to partner with automation and tech-solution experts when pursuing digital transformation.
How Innovior approaches digital transformation
Digital transformation in heavy industries does not require a company to complete a total overhaul of its technology stack or disrupt current workflows. At Innovior, we know every business is unique and that means every business requires a tailored approach to get the most out of their innovative solutions … and this is how we do it.
- Discovery process: our journey begins with an in-depth discovery phase, which typically lasts from a couple of days to a fortnight depending on business complexity and sees us collaborate closely with clients to identify the core issues and root causes underlying their operational challenges. This phase often uncovers surprising insights that reshape our understanding of the problem statement.
- Ground-level insights: we believe in getting our hands dirty and engaging directly with frontline staff to gain a holistic understanding of the existing processes. By mapping out the actual workflows and soliciting feedback from those directly involved, we unearth valuable insights that inform our approach.
- Lean Six Sigma principles: drawing upon Lean Six Sigma methodologies, we meticulously analyse the mapped processes to identify inefficiencies, eliminate waste and uncover opportunities for automation. By aligning our efforts with our clients' key metrics and objectives, we ensure our solutions deliver tangible results.
- Optimal approach: we recognise the inherent uniqueness of each organisation and avoid adopting a one-size-fits-all approach. By tailoring our solutions to address the specific pain points and challenges faced by our clients, we strike a thoughtful balance between configuration and customisation where necessary to avoid technical debt and platform support costs.
- End-to-end transformation: we offer comprehensive transformation solutions that encompass the entire lifecycle of a process, from analysis and design to implementation and optimisation. Our goal is not just to deliver quick fixes but facilitate lasting change that drives sustainable growth and performance improvement.
- Best-of-breed technology: we pride ourselves on our ability to leverage a diverse range of tools and technologies to design solutions that best fit our clients’ needs. From Microsoft PowerPlatform and robotics process automation to Salesforce and Service Now, we prioritise outcomes over specific platforms or solutions and leverage best-of-breed technology to deliver results.
- Flexibility, rapid delivery and quality: we understand the need for agility and adaptability in today’s fast-paced business environment. Our nimble approach incorporates rapid prototyping and agile methodologies that enable us to deliver results quickly, with a typical cycle from initial discovery to the delivery of solutions spanning just 6-8 weeks. This rapid turnaround time allows our clients to realise tangible benefits in a short timeframe and lays the groundwork for larger-scale transformations. Even when addressing a focused problem statement, we prioritise alignment with the overarching organisational strategy or roadmap to ensure optimal outcomes.
- Enhancing user experience: in the realm of heavy industries, the importance of user experience often goes unnoticed during solution development. Our approach diverges from this oversight, as we prioritise not only enhancing business processes but also optimising user experiences. Recognising that inefficiencies and frustrations can arise from overlooking usability, we actively engage frontline staff in our design process. This ensures our solutions not only deliver functionality but also offer a seamless and user-friendly experience, ultimately resulting in heightened satisfaction and efficiency.
- Industry and technology experience: at our core, we offer a distinct advantage and that is we not only understand the technology landscape but have ample experience in delivering digital transformation projects within heavy industries led by seasoned engineers who possess firsthand knowledge of their respective domains. We have a proven track record of delivering intelligent automation solutions that have saved several million dollars in the heavy industries while implementing robust re-engineered processes that drive efficiency and operational excellence.
Ultimately, the reason clients appreciate working with us is our consulting-first approach. We fully understand the business problem, leverage the best-of-breed technologies in our repertoire and by combining our comprehensive industry and technological acumen, we empower organisations to seamlessly navigate the complexities of digital transformation.
An example of digital transformation
In recent times, a leading oil and gas company approached us with a not-so-simple request – to help cut its costs by more than 10% through process improvement and automation. Those were clearly big numbers but we are not afraid of a challenge. From land access, drilling and completions to finance and people and culture, we carried out a detailed investigation of core business processes to identify cost-saving opportunities that led to more than 23 processes being automated and the establishment of a Transformation Centre of Excellence.
The result? A five-time return on investment that has enabled greater efficiency and cost reduction across the organisation.
This is not an isolated case. Automation and digital transformation are an untapped resource for many players in the heavy industry and, with the guiding hand of specialists well versed in the field, there is no reason the journey to more efficient and profitable processes cannot start today.
To learn more about how Innovior can help transform your business systems, contact us today.
Generative AI has been one of the most hyped technologies of recent years but that does not mean it is suitable for all businesses. Discover the generative AI limitations that may inspire organisations to invest their time and money elsewhere.
[1] Digital Maturity Consulting and Strategy | BCG
[2] Racing Toward a Digital Future in Metals and Mining | BCG
[3] The imperative to automate business processes | McKinsey